Moisture intrusion is one of the primary causes of a roof’s structural issues. One element that’s impacting moisture in the roofing system is the drive toward energy efficiency and the resulting increase in conditioned attic spaces. This shift adds to the already well-known sources of water—namely, weather—and brings heightened concerns about moisture accumulation on the roof and penetration of the roof deck.
Let’s discuss the effects of unwanted moisture and explore strategies for installers to prevent its adverse effects.
How Does Moisture Reach the Roof Deck?
While it’s a common belief that shingles, coupled with an underlayment, form an impenetrable barrier against moisture reaching the sheathing, we always want to operate under the assumption that moisture will get where we don’t want it to. There are two scenarios in which water or vapor can infiltrate the roof deck –– both from the exterior and interior.
1. Exterior
Water typically finds its way to the roof deck through a compromised underlayment, a common vulnerability in roofing systems. But that’s not the only way. Mechanically attached roofing underlayments, despite their utility, introduce potential pitfalls such as nail holes and a discontinuous layer that trapped moisture can seep through, leading to the saturation of the sheathing. Once the sheathing is damp, conventional non-permeable underlayments hinder the drying process, resulting in structural degradation over time.
Recognizing this challenge, Benjamin Obdyke pioneered the first-of-its-kind continuous-acrylic, vapor-permeable underlayment—Vapor Dry SA. With vapor-permeable options like Vapor Dry SA, moisture can dissipate, promoting drying through the roofing system. In contrast, non-permeable alternatives impede the drying process, allowing moisture to linger and contribute to long-term deterioration of the sheathing.
2. Interior
Interior moisture is a byproduct of routine activities such as talking, showering, cooking, and the presence of indoor plants. As hot air rises, it carries moisture with it. This moisture can build up and become trapped by a non-permeable, vapor-closed synthetic roofing underlayment.
Signs of Moisture Damage on the Roof
One tricky thing about roof damage from moisture is that it’s not easy to notice. That’s why as builders, it’s crucial to plan with the idea that moisture will infiltrate those areas and cause damage. If we prepare for the worst, we can ensure the best.
In some cases, the homeowner may see the paint on the ceiling start to bubble and the drywall or finishes to delaminate. Any building material that consistently maintains a high saturation point or moisture content will grow mold, and the signs of mold are some of the biggest indicators of moisture failure in the system. The true damage reveals itself once you take the assembly apart. It doesn’t take a large volume of moisture to cause this damage — interior building materials are not designed to withstand wetting events.
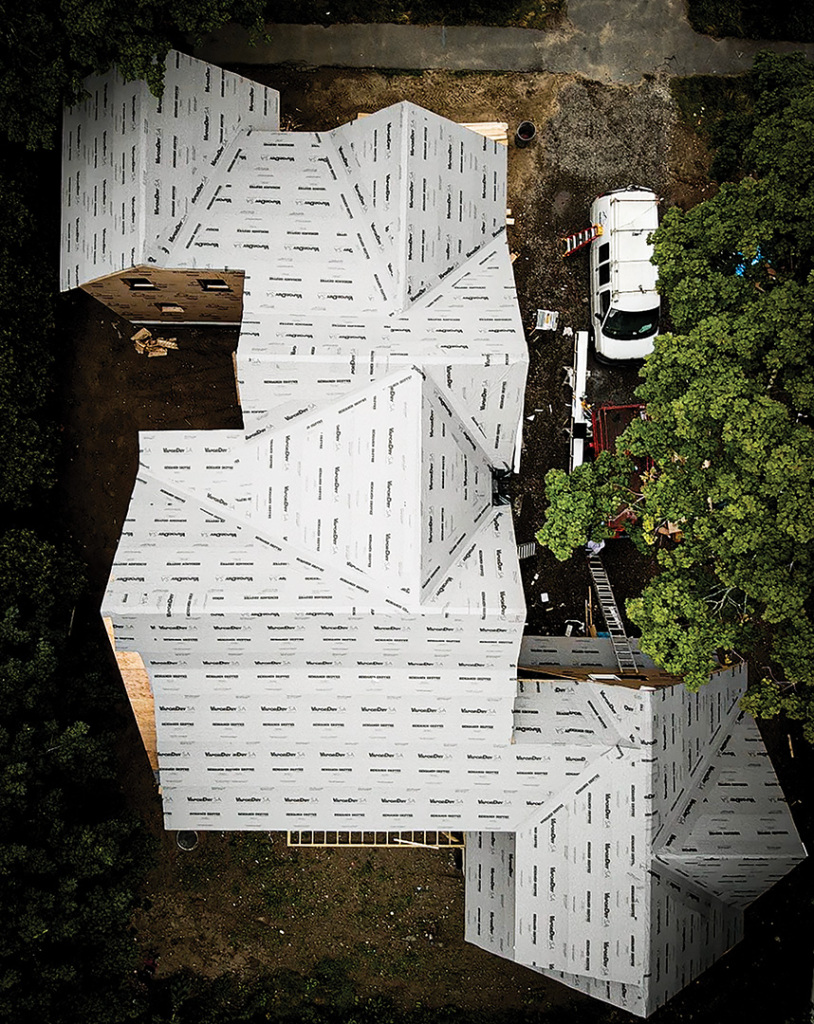
VaporDry® SA Samples
GET YOUR FREE VAPORDRY® SA SAMPLES TODAY
Effects of Moisture Build Up on the Roof
As the focus shifts toward air-tight homes and enhanced energy efficiency, the resulting changes to our building envelope assemblies are raising concerns about indoor air quality for occupants and natural drying potential for building envelope. The push for tightly sealed, energy-efficient homes inadvertently restricts the natural movement of fresh air; in the attic, this lack of ventilation can allow moisture to build up in the roof system, leading to mold, rot, and other microbial organism growth, increasing the risk of products or the whole system failing.
In contrast, historic or vintage homes, with their drafts and leaks, naturally bring in fresh air, enhancing the overall drying potential of the entire structure. Ultimately, the primary objective in the building industry is to create spaces where people can live, work, and play safely and healthily.
What You Should Know as an Installer
When it comes to working on the roof and understanding these complex details and code changes, it’s vital to ask questions ahead of time. The complexities of our building installations are changing the way we approach projects. Before arriving at the jobsite, it’s important to talk about these details and look at the entire building envelope and evaluate how everything is designed to work together. Addressing potential modifications early in the process is more effective than making adjustments during installation. This approach ensures that installers receive proper education on the specifics and execute installations with precision—a proactive stance versus a reactive one.
Implementing proactive measures should include preconstruction meetings with architects, installers, contractors, manufacturers, and builders. Local training events from manufacturers and product representatives can teach installers and contractors proper techniques, providing hands-on experience along with the opportunity to ask questions in real time.
Benjmain Obdyke currently hosts collaborative contractor training events for anyone interested in attending. Contact us for more information.
As we strive for perfection in the building envelope, our increased emphasis on efficiency has reduced the resiliency of our structures. Small leaks or elevated moisture levels pose a threat, as our building materials lack the drying potential present in old structures. It is imperative that we acknowledge this challenge and provide proper training and products for installers to address the evolving demands of construction to avoid failures.
Subscribe to stay up to date or request a virtual jobsite visit to help ensure you know how everything is designed to work together.