When it comes to best practice guidelines for the roof, inconsistency is a common theme. Roofing practices have long suffered from a lack of standardized guidelines, leading to varied quality and performance. This gap in regulation often results in confusion among contractors and builders—and a greater chance of failures.
The roof is both one of the most vulnerable parts of the home and one of the most complicated to get right. Yet, guidelines and standards haven’t always kept up with new technologies and better methods.
Building codes provide an outline of basic materials to use and address common roof details like eave drip edges, roof-to-wall intersections, and crickets. However, the majority of roof replacements do not need to have a code official involved. This can lead to problems as roofers may cut corners trying to be the cheapest bid to earn the reroof job.
Industry associations offer training programs, but they aren’t always current with the latest building science or product technologies.
In addition, following the codes represents the minimum requirements. Often, greater efficiency and higher performance can be achieved by building above code.
Why Is a Lack of Stronger Roofing Guidelines an Issue?
Without building-science-based guidelines, the go-to and/or lowest-cost methods often prevail, which can lead to improper construction and eventually roof failure, leaking, rot, and poor energy efficiency. Not understanding the building envelope control layers and ventilation strategies also may cause poor indoor air quality. Reverse flashing or improper transitions can create leaks and callbacks. The challenges are numerous.
One growing area of concern is that the building code does not require vapor permeance in roofing membranes. It is best practice to allow interior moisture to dry up and out but traditional synthetic underlayments do not allow this. Vapor-permeable, self-adhered underlayment such as VaporDry SA creates long-term protection based on building science and real-world applications. It also combines the self-sealing feature of a self-adhered ice barrier with the vapor permeance of a felt paper.
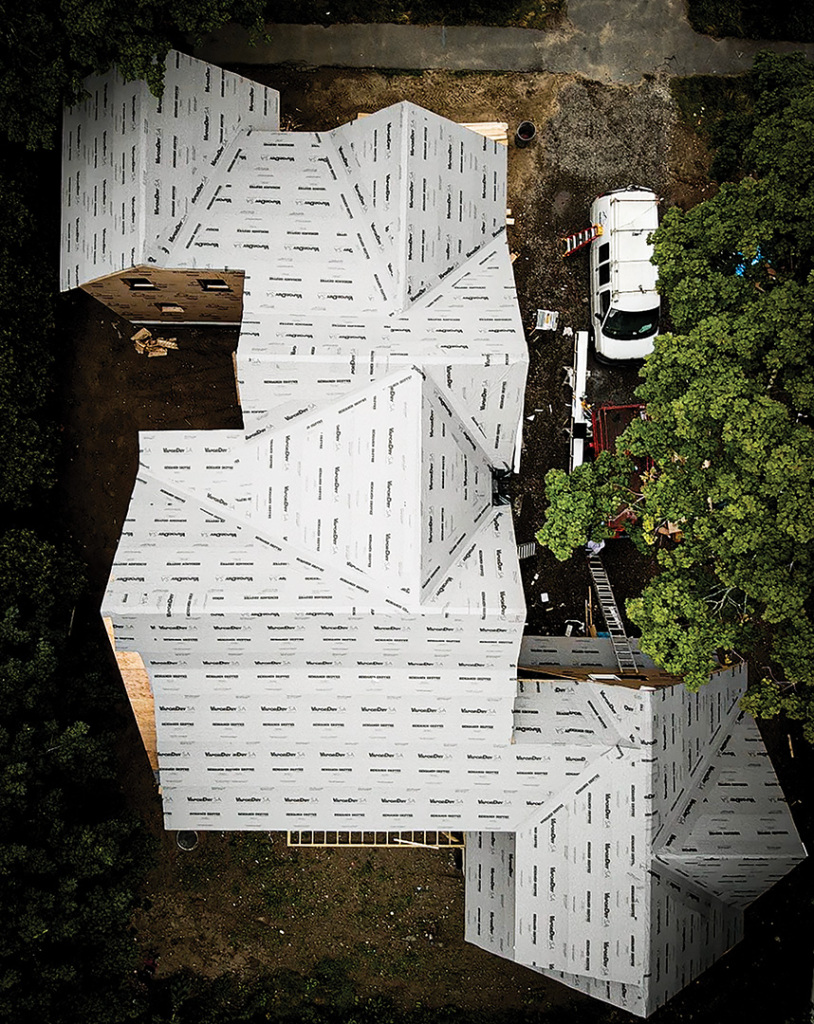
VaporDry® SA Samples
GET YOUR FREE VAPORDRY® SA SAMPLES TODAY
Another best practice not required by code is, just like a wall, adding an air gap above a vapor-permeable membrane, which allows for the maximum drying potential of the roof assembly. This can be created with cross-bracing or strapping that is tied into the eave and ridge ventilation. For a more detailed look at strapping, read Best Practices for Double Strapping the Roof.
Similarly, the industry’s slow standardization of new technologies can inhibit new best practices. For example, there are no ASTM standards that address acrylic adhesives like those used for VaporDry SA; the adhesive was developed over five years and offers the ideal combination of repositionability and long-term adhesion after pressure is applied.
Traditional asphaltic self-adhered ice barriers require a minimum thickness of adhesive to achieve the basic performance standards, like fastener sealability. Acrylic products can outperform conventional adhesives with less adhesive and offer more advanced features and benefits.
How Can Contractors Combat Slow Standardization?
As with other areas of the envelope, it’s vital for builders, remodelers, architects, and roofers to think beyond code. Understand the science behind proper installation and work with manufacturers to weigh the benefits of new technologies. Combine code requirements with high-performance products and better, science-based building practices. And look to building science and manufacturer support to stay at the forefront of high-quality installation. to stay at the forefront of high-quality installation. In turn, educate homeowner customers on why a slightly higher investment in a better-built roof will lead to long-term savings and peace of mind down the road.
Benjamin Obdyke is here to help you elevate your practices based on the latest building science. Check out our library of resources and educational materials, and sign up for a virtual jobsite visit to get started.